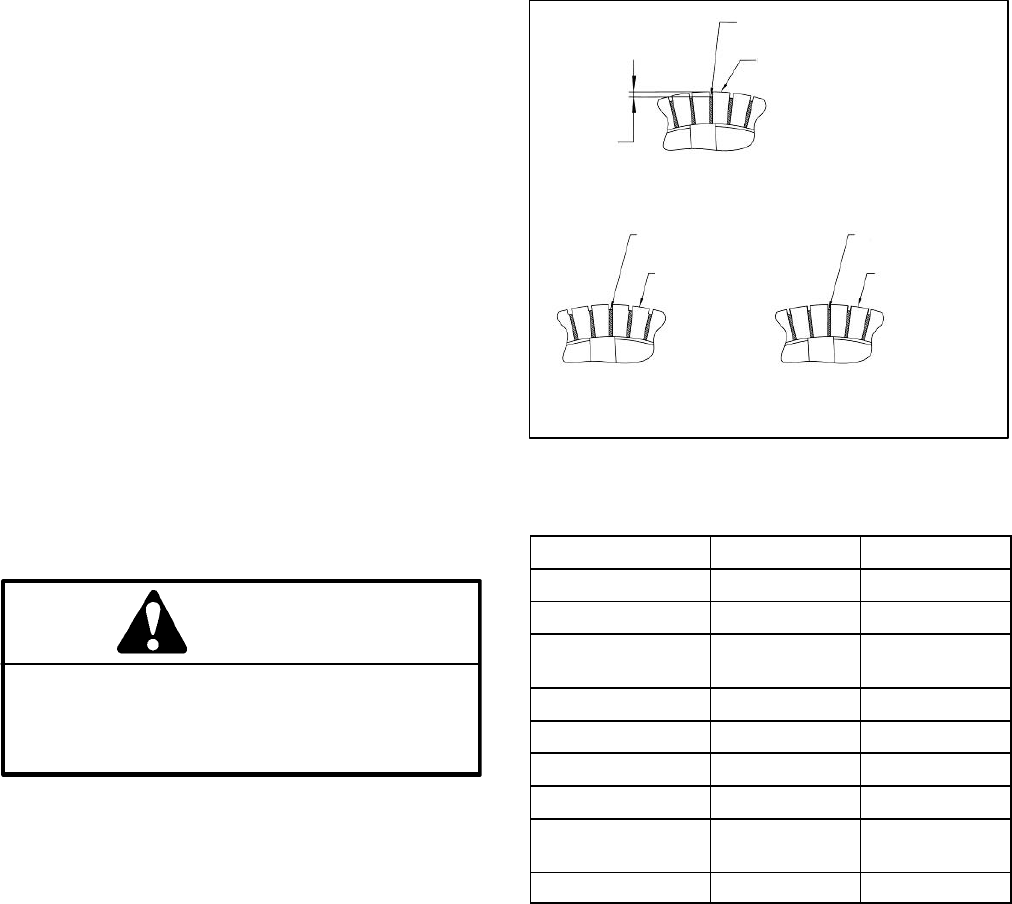
Workman e2050/e2065
Page 3 – 40
Electrical System (Rev. B)
Commutator Service
1. Chuck armature on the commutator end–bearing
journal and support the drive end of armature using the
”live” center of the shaft. With the armature supported on
both ends, measure the commutator runout and the bar
to bar differences with a dial gauge. Total indicated run-
out should not exceed 0.003” (0.08 mm) and not more
than 0.0005” (0.013 mm) between any two bars. If the
readings fall outside this limit, the commutator must be
turned and re–undercut.
2. If the commutator must be turned, use only high
quality cutting tools with a controlled cutting rate. Re-
move only enough copper to bring total indicated runout
and bar to bar height differences into specification.
3. The minimum commutator diameter is 2.750” (70
mm). If the commutator diameter falls below this diame-
ter after turning, the armature must be replaced.
4. After the commutator is turned, undercut the mica to
a uniform depth of 0.040” (1.0 mm). Be careful to only cut
the mica and not increase the slot width (Fig. 61).
CAUTION
When using compressed air for cleaning mo-
tor components, follow all safety instructions,
including wearing eye and respiratory protec-
tion.
5. After undercutting, use No. 00 sandpaper to lightly
remove any burrs left from the undercutting operation.
Clean commutator with dry, oil free compressed air and
recheck commutator runout.
Armature Testing
Before an armature is reassembled into the motor, the
following tests should be performed:
NOTE: Armature is wave wound and can be short cir-
cuit tested in the following manner.
1. Check for grounded circuits by placing one test lead
of a dielectric tester on the commutator and the other
lead at the armature shaft. If the test light comes on, the
armature is grounded.
2. Check for short circuits by placing the armature on a
growler. Use a long, flat piece of metal (such as a hack-
saw blade) to locate any shorted windings.
If armature is found to be shorted, grounded or other-
wise damaged, replace the traction motor.
Figure 61
MICA
GOOD UNDERCUT
COPPER SEGMENT
MICA MICA
COPPER SEGMENT
BAD UNDERCUT BAD UNDERCUT
(CUT TOO WIDE) (CUT TOO NARROW)
COPPER SEGMENT
.040”
(1.0 mm)
Traction Motor Specifications
BRUSH LENGTH
Maximum 1.300 in 33 mm
Minimum 0.620 in 16 mm
BRUSH SPRING
TENSION
New Brush 65 ounces 1820 grams
Worn Brush 40 ounces 1120 grams
COMMUTATOR
New Diameter 2.920 in 74 mm
Minimum Diame-
ter for Reslotting
2.800 in 71 mm
Reject Diameter 2.750 in 70 mm