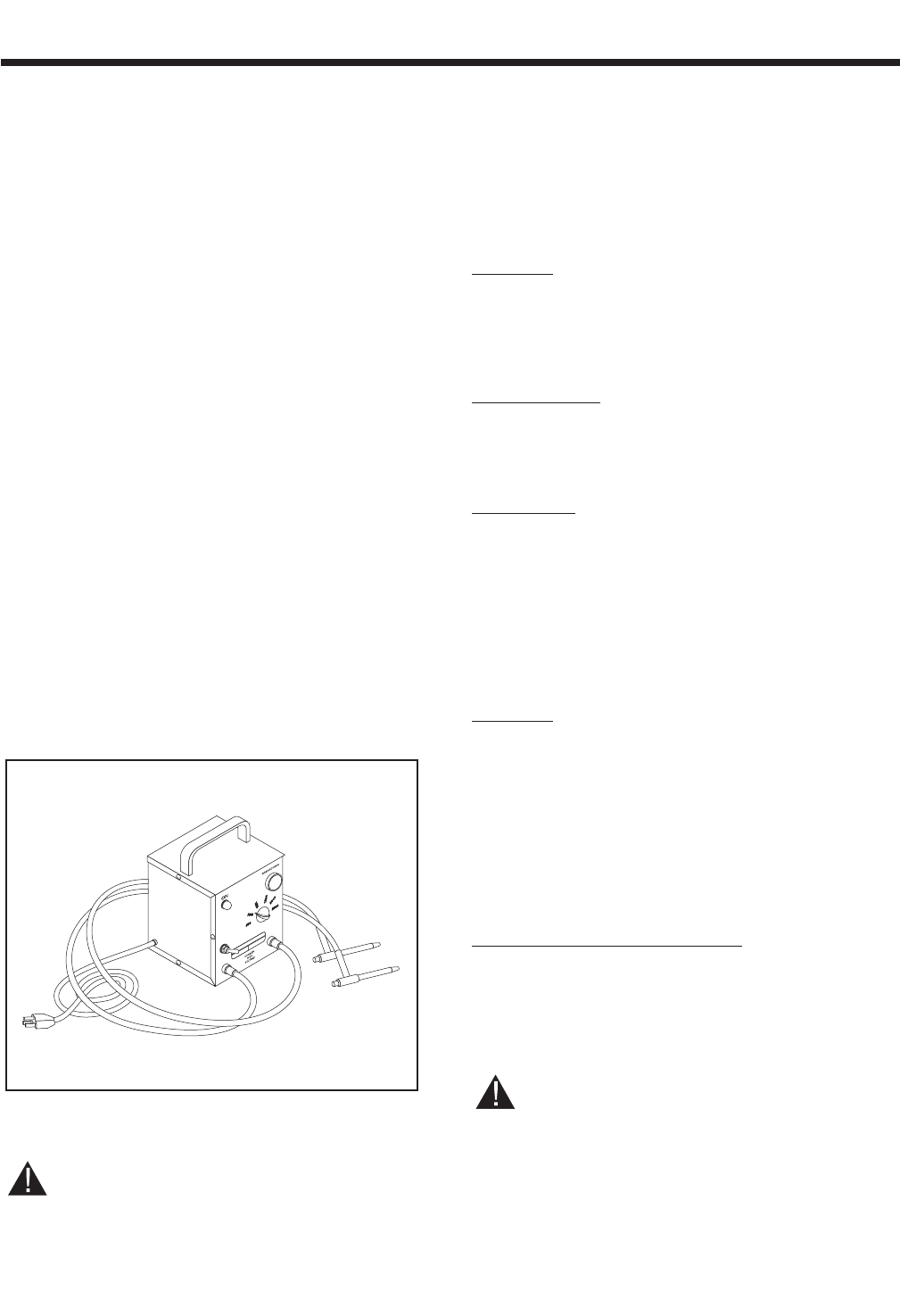
Section 3
INSULATION RESISTANCE TESTS
EFFECTS OF DIRT AND MOISTURE
Moisture and dirt are harmful to the continued good
operation of any generator set.
If moisture is allowed to remain in contact with the
Stator and Rotor windings, some of the moisture will
be retained in voids and cracks of the winding insula-
tion. This will result in a reduced insulation resistance
and, eventually, the unit's AC output will be affected.
Insulation used in the generator is moisture resistant.
However, prolonged exposure to moisture will gradu-
ally reduce the resistance of the winding insulation.
Dirt can enhance the problem, since it tends to hold
moisture into contact with the windings. Salt, as from
sea air, contributes to the problem since salt can
absorb moisture from the air. When salt and moisture
combine, they make a good electrical conductor.
Due to the detrimental affects of dirt and moisture, the
generator should be kept as clean and as dry as pos-
sible. Rotor and Stator windings should be tested
periodically with an insulation resistance tester (such
as a megohmmeter or hi-pot tester).
If the insulation resistance is excessively low, drying
may be required to remove accumulated moisture.
After drying, perform a second insulation resistance
test. If resistance is still low after drying, replacement
of the defective Rotor or Stator may be required.
INSULATION RESISTANCE TESTERS
Figure 3-1 shows one kind of hi-pot tester. The tester
shown has a “Breakdown” lamp that will glow during
the test procedure to indicate an insulation break-
down in the winding being tested.
Figure 3-1. – One Type of Hi-Pot Tester
DANGER! INSULATION RESISTANCE
TESTERS SUCH AS HI-POT TESTERS AND
MEGOHMMETERS ARE A SOURCE OF HIGH
AND DANGEROUS ELECTRICAL VOLTAGE.
FOLLOW THE TESTER MANUFACTURER'S
INSTRUCTIONS CAREFULLY. USE COMMON
SENSE TO AVOID DANGEROUS ELECTRICAL
SHOCK
DRYING THE GENERATOR
GENERAL:
If tests indicate the insulation resistance of a winding
is below a safe value, the winding should be dried
before operating the generator. Some recommended
drying procedures include (a) heating units and (b)
forced air.
HEATING UNITS:
If drying is needed, the generator can be enclosed in
a covering. Heating units can then be installed to
raise the temperature about 15°-18° F. (8°-10° C.)
above ambient temperature.
FORCED AIR:
Portable forced air heaters can be used to dry the
generator. Direct the heated air into the generator’s
air intake openings. Remove the voltage regulator
and run the unit at no-load. Air temperature at the
point of entry into the generator should not exceed
150° F. (66° C.).
CLEANING THE GENERATOR
GENERAL:
The generator can be cleaned properly only while it is
disassembled. The cleaning method used should be
determined by the type of dirt to be removed. Be sure
to dry the unit after it has been cleaned.
NOTE: A shop that repairs electric motors may be
able to assist you with the proper cleaning of gen-
erator windings. Such shops are often experi-
enced in special problems such as a sea coast
environment, marine or wetland applications,
mining, etc.
USING SOLVENTS FOR CLEANING:
If dirt contains oil or grease a solvent is generally
required. Only petroleum distillates should be used to
clean electrical components. Recommended are
safety type petroleum solvents having a flash point
greater than 100° F. (38° C.).
CAUTION!: Some generators may use epoxy
or polyester base winding varnishes. Use sol-
vents that will not attack such materials.
Use a soft brush or cloth to apply the solvent. Be
careful to avoid damage to wire or winding insulation.
After cleaning, dry all components thoroughly using
moisture-free, low-pressure compressed air.
Page 12