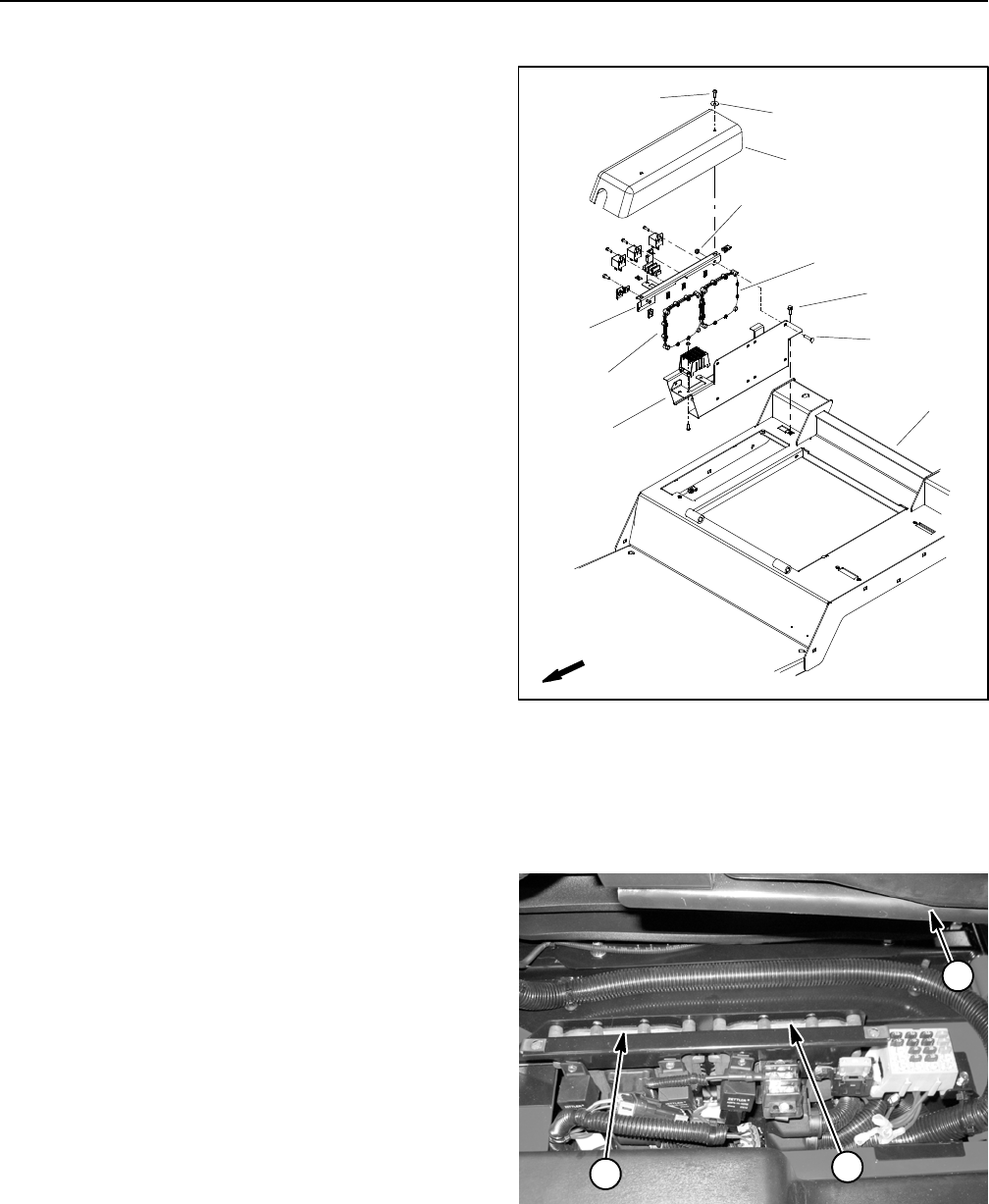
Groundsmaster 4000--D/4010--DPage 5 -- 50Electrical System
Toro Electronic Controllers (TEC)
Groundsmaster4000--D and4010--D machines usetwo
(2)ToroElectronic Controllers (TEC)to control electrical
system operation. The controllers are attached to the
operator platform under the controller cover (Figs. 64
and 65).
Logic power is provided to the controllers as long as the
battery cables are connected to the battery. A pair of 2
Amp fuses (fuse D--1 for the front controller and fuse
D--2 for the rear controller) provide circuit protection for
this logic power to the controllers.
The front TEC controller monitors the states of the fol-
lowing components as inputs: ignition switch, traction
pedal position sensor , parking brake switch, HI/LOW
speed switch, service brake switches, seat switch, en-
gine speed switch, hydraulic temperature sender, turn
signal switch (if equipped) and hazard switch (if
equipped).
The front TEC controller controls electrical output t o the
engine ECU (start and run functions), fan drive solenoid
coils (direction and flow source), traction (piston) pump
solenoids (forward and reverse) and traction solenoid
coil (HI/LOW speed). Additionally, electrical outputs for
brake lights, turn lights and warning lights on Grounds-
master 4010--D machinesare provided bythe front TEC
controller. Circuit protection for front TEC outputs ispro-
vided by three (3) 7.5 Amp fuses (fuse locations A--1,
B--1 and C--1).
The rear TEC controller monitors the states of the fol-
lowing components as inputs: ignition switch, cutting
deck lift switches, PTO switch, cruise control switch and
deck position switches.
The rear TEC controller controls electrical output to the
PTO solenoidcoils, lift/lower solenoid coilsand fan drive
solenoid coil (speed). Circuit protection for rear TEC
outputs is provided by three (3) 7.5 Amp fuses (fuse loc-
ations A--2, B--2 and C--2).
The InfoCenter display should be used to check inputs
and outputsof the TEC controllers.Information onusing
the InfoCenteris included in the InfoCenter Display sec-
tion of this chapter.
The diagram in Figure 66 depicts the connection termi-
nal functionsfor the TEC controllers. Note that electrical
powerfor controlleroutputs isprovidedthrough three(3)
connectors(PWR 2,PWR 3and PWR 4)each protected
witha 7.5 ampfuse. Afifty (50) pinwire harnessconnec-
tor attaches to the controller. The connector pins are
identified in the diagram in Figure 66. The layout of the
wire harness connectors that plug into the TEC control-
lersisshowninFig.67.
1. Controller cover
2. Screw (2 used)
3. Flat washer (2 used)
4. Flange screw (2 used)
5. Power mount
6. Relay mount
7. Carriage screw (8 used)
8. Flange nut (8 used)
9. Front TEC controller
10. Rear TEC controller
11. Operator platform
Figure 64
FRONT
2
3
7
1
6
4
5
8
9
10
11
1. Front TEC controller
2. Rear TEC controller
3. Operator seat
Figure 65
2
1
3