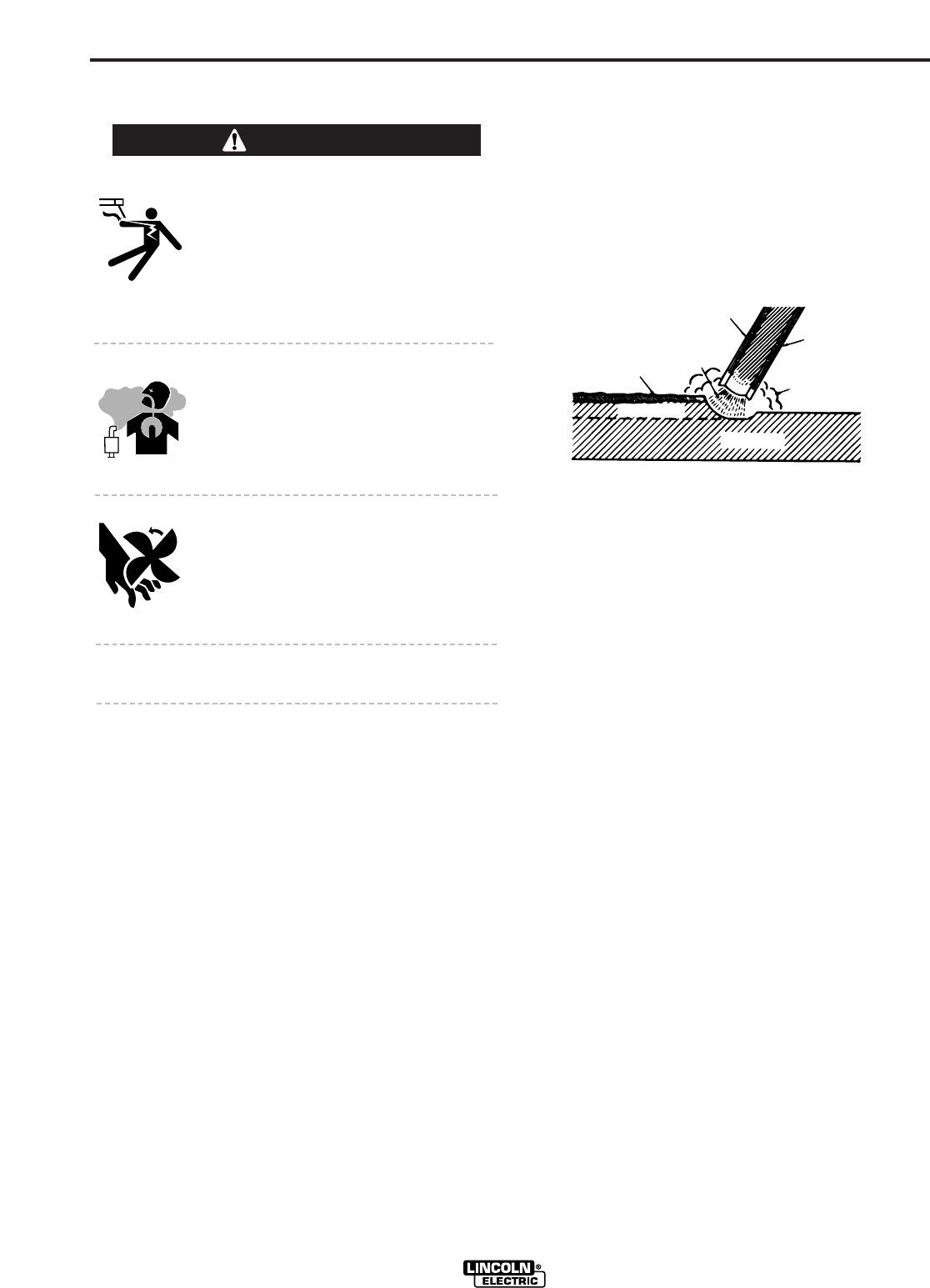
B-12
OPERATION
B-12
POWER-ARC 4000
The Power-Arc 4000 has a voltage output of up to 62
volts which can shock.
The electric arc is made between the work and the tip
end of a small metal wire, the electrode, which is
clamped in a holder that is held by the welder. A gap
is made in the welding circuit (see Figure 3) by hold-
ing the tip of the electrode 1/16 - 1/8” (1.6-3.2mm)
away from the work or base metal being welded. The
electric arc is established in this gap and is held and
moved along the joint to be welded, melting the metal
as it is moved.
Arc welding is a manual skill requiring a steady hand,
good physical condition, and good eyesight. The
operator controls the welding arc and, therefore, the
quality of the weld made.
What Happens in the Arc?
Figure 4 illustrates the action that takes place in the
electric arc. It closely resembles what is actually seen
during welding.
The “arc stream” is seen in the middle of the picture.
This is the electric arc created by the electric current
flowing through the space between the end of the
electrode and the work. The temperature of this arc is
about 6000°F (3316°C) which is more than enough to
melt metal. The arc is very bright, as well as hot, and
cannot be looked at with the naked eye without risking
painful and possibly permanent injury. A very dark
lens, specifically designed for arc welding must be
used with the handshield or headshield whenever
viewing the arc.
The arc melts the base metal and actually digs into it,
much like water through a garden hose nozzle digs
into the earth. The molten metal forms a pool or
crater and tends to flow away from the arc. As it
moves away from the arc, it cools and solidifies. Slag
forms on top of the weld to protect it during cooling.
The function of the covered electrode is much more
than simply to carry current to the arc. The electrode
is composed of a core metal wire around which has
been extruded and baked a chemical covering. The
core wire melts into the arc and tiny droplets of molten
metal shoot across the arc into the molten pool. The
electrode provides additional filler metal for the joint to
fill the groove or gap between the two pieces of the
base metal. The covering also melts or burns in the
arc. It has several functions. It makes the arc stead-
ier, provides a shield of smoke-like gas around the arc
to keep oxygen and nitrogen in the air away from the
molten metal, and provides a flux for the molten pool.
The flux picks up impurities and forms a protective
slag. The principle differences between the various
types of electrodes are in their coatings. By varying
the coating, it is possible to greatly alter the operating
characteristics of electrodes. By understanding the
differences in the various coatings, you will gain a bet-
ter understanding of selecting the best electrode for
the job you have at hand. In selecting an electrode,
you should consider:
1. The type of deposit you want, e.g., mild steel,
stainless, low alloy, hardfacing.
2. The thickness of the plate you want to weld.
3. The position it must be welded in (downhand,
out-of-position).
4. The surface condition of the metal to be welded.
5. Your ability to handle and obtain the desired
electrode.
Four simple manipulations are of prime importance.
Without complete mastery of these four, further
attempts at welding are futile. With complete mastery
of the four, welding will be easy.
ELECTRIC SHOCK can kill.
• Do not touch electrically live parts
or electrode with skin or wet cloth-
ing.
• Insulate yourself from work and
ground.
• Always wear dry insulating gloves.
WARNING
ENGINE EXHAUST can kill.
• Use in open, well ventilated areas
or vent exhaust outside.
• Do not stack anything on or near
the engine.
MOVING PARTS can injure.
• Do not operate with doors open or
guards off.
• Stop engine before servicing.
• Keep away from moving parts.
Only qualified personnel should install, use, or
service this equipment.
Covering
Electrode
Shielding Gases
Arc
Solidified Slag
Weld Metal
Base Metal
FIGURE 4 - The welding arc.