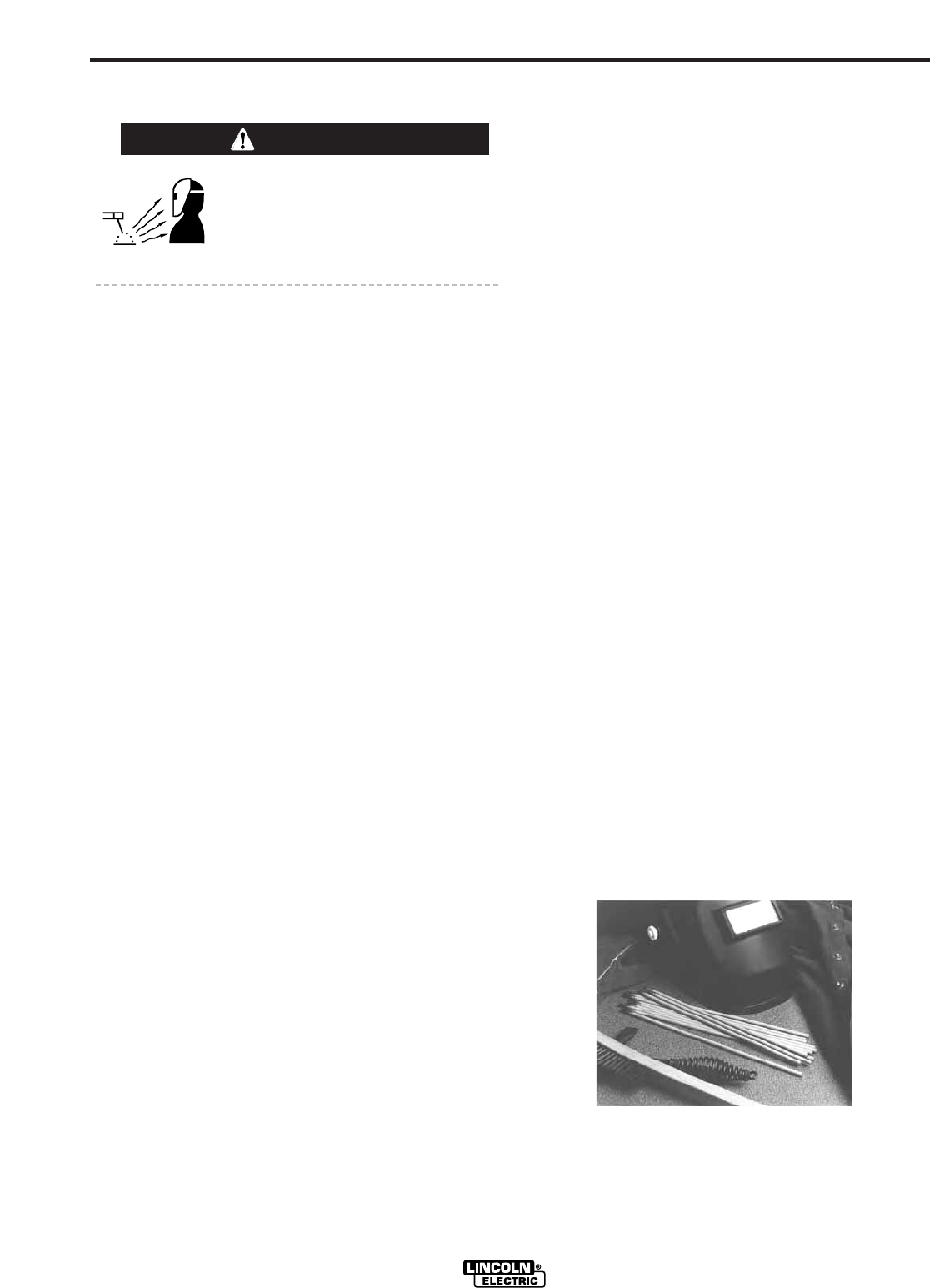
B-11
OPERATION
B-11
POWER-ARC 4000
Stick welding is probably the most familiar welding
process known. A coated ELECTRODE, the weld
rod, is clamped into an ELECTRODE HOLDER, an
insulated clamping device, which in turn connects to
the ELECTRODE CABLE, a heavy wire. The WORK,
the metal piece to be welded, is connected to the
WORK CABLE, a heavy wire which contains the
WORK CLAMP. Quality Lincoln cables use many fine
copper wires with a very flexible insulating covering
for the electrode and work cables. When properly con-
nected to the OUTPUT STUDS of a high current
power source, the electrode melts and bonds the
metal being repaired. Refer to Figure 3 to see the cir-
cuit. See “Cable Installation” section for proper cable
connection to a Power-Arc.
The Power-Arc provides excellent weld output charac-
teristics when used in combination with Lincoln AC
electrodes. Other AC electrodes may also be used.
Follow the settings listed in Table 2 “Welding
Application Chart” and the “Electrode Selection Guide”
found on the nameplate of the machine.
ARC RAYS can burn.
• When using an open arc process,
it is necessary to use correct eye,
head and body protection.
WARNING
Stick Welding
Semi-automatic, MIG Welding With a
Lincoln Weld Pak 100 or Weld Pak 125
The Power-Arc generator power can be used to supply
power to a Lincoln Weld-Pak 100 or Weld-Pak 125 wire
feed welder.
The Weld-Pak is equipped with all the
supplies needed for Flux-Cored Arc Welding (FCAW),
and is available where Lincoln products are sold.
A K610-1 MIG Conversion Kit is also available for the
Weld-Pak which provides all the essentials needed for
Gas Metal Arc Welding, GMAW, or MIG processes.
Contact your local authorized Lincoln representative
for
more details.
Learning To Stick Weld
The serviceability of a product or structure utiliz-
ing this type of information is and must be the
sole responsibility of the builder/user. Many vari-
ables beyond the control of The Lincoln Electric
Company affect the results obtained in applying
this type of information. These variables include,
but are not limited to, welding procedure, plate
chemistry and temperature, weldment design, fab-
rication methods and service requirements.
No one can learn to weld simply by reading about it.
Skill comes only with practice. The following pages
will help the inexperienced welder understand welding
and develop his skill. For more detailed information,
order a copy of the book “New Lessons in Arc
Welding.”
(See Book Division section at rear of manual).
The operator’s knowledge of arc welding must go
beyond the arc itself. He must know how to control the
arc, and this requires a knowledge of the welding cir-
cuit and the equipment that provides the electric cur-
rent used in the arc. Figure 3 is a diagram of the weld-
ing circuit. The circuit begins where the electrode
cable is attached to the welding machine and ends
where the work cable cable is attached to the
machine. Current flows through the electrode cable to
the electrode holder, through the electrode holder to
the electrode and across the arc. On the work side of
the arc, the current flows through base metal to the
work cable and back to the welding machine. The cir-
cuit must be complete for the current to flow. To weld,
the work clamp must be tightly connected to clean
base metal. Remove paint, rust,etc. as necessary to
get a good connection. Connect the work clamp as
close as possible to the area you wish to weld. Avoid
allowing the welding circuit to pass through hinges,
bearings, electronic components or similar devices
that can be damaged.