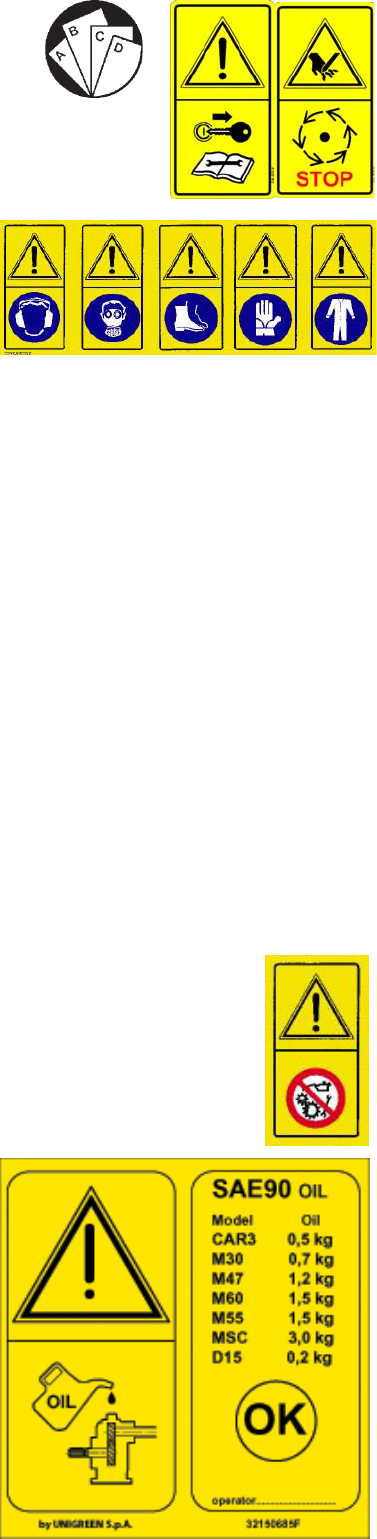
22 unigreen
8 MAINTENANCE
All of the maintenance operations and repairs must be carried out with the ma-
chine and cardan shaft stopped and the tank and circuit clean of any residues
of chemical products.
The maintenance of the atomiser is essential for maintaining a high level of
safety. Also consult the single handbooks of the main components of the atom-
iser.
8.1 PROGRAMMED MAINTENANCE
(TAB. N° 7, page 36)
We recommend using a table of programmed maintenance to follow in time to
keep the atomiser in an efficient working condition.
For major and important maintenance jobs we recommend using the normal
UNIGREEN assistance service available from your reseller, (if necessary)
replacing parts using original spare parts only.
8.2 ROUTINE MAINTENANCE
= After every treatment wash the inside of the tank and the entire circuit as
indicated in paragraph 4.13
= Periodically check that the suction and delivery filters are clean
= Check the oil level in the volumetric compensator of the pump
= The use of chemical products that are particularly damaging for a nitrile
rubber mix can cause the diaphragm to break before time.
In these conditions check the state of the components more often. There are
diaphragms made of special materials (viton and desmopan) that are available
on request.
= When doing treatments with copper hydroxide you should take great care
to thoroughly clean the system, washing it after each treatment because
hydroxides attack parts that aren’t painted or protected by hot galvanising.
To prevent chemical attacks we recommend spraying transparent paint on the
parts that are most exposed to the product and equipping the atomiser with
stainless steel pressure gauges.
8.2.1 CLEANING THE NOZZLES
Check the state of wear of the nozzles and replace them when the delivery is
over 30-35% of the theoretical level.
If you notice even a partial blockage of a nozzle proceed as follows:
- drain the pressure and stop the machine
- dismantle the screw or bayonet ringnuts holding the nozzles
- clean with a small brush or compressed air, don’t use nails, punches or
bradawls
- reassemble the nozzles and the ringnuts, replacing the filters and seals.
8.2.2 LUBRICATION
The moving mechanical components must be lubricated to prevent wear and
overheating. This lubrication can be done with grease or oil: oil allows
significantly higher speeds, in general grease is used to lubricate bearings with
a vertical or inclined axis as it stays in the zone for longer.
8.2.3 MULTIPLIER LUBRICATION
The multiplier and disengaging boxes are normally lubricated in an “oil bath”, in
special cases NLGI n.0 grease is used. The viscosity is an essential
characteristic of a lubricant oil and this is indicated by the SAE (SOCIETY OF
AUTO-MOTIVE ENGINEERS) classification of the oils for gearboxes and
differentials. Special additives improve the capacity of the oil to maintain a
lubricant film also at high pressures and temperatures. We recommended using
SAE 90 oil for the multiplier and disengaging boxes. The quantity of oil is
established by the level cap. A greater quantity of oil doesn’t improve the
conditions of lubrication and can cause overheating in the box. Changing the oil
protects the parts from the dangers associated with wear and the presence of
metallic particles that can be present, especially in the first period of use. We
recommend replacing the oil after the first 50 working hours and then
subsequently every 500 hours.
The quantity of oil needed is indicated on the sticker near the multiplier (FIG.
23)
WARNING: the oil used mustn’t be dispersed in the environment and must
be collected the relevant containers.
8.3 EXTRAORDINARY MAINTENANCE
At the end of a season of intense use, or every two years of normal use, it is a
good idea to have a specialised service technician perform a general check on
the machine.
8.4 REPAIRS
FIG. 29