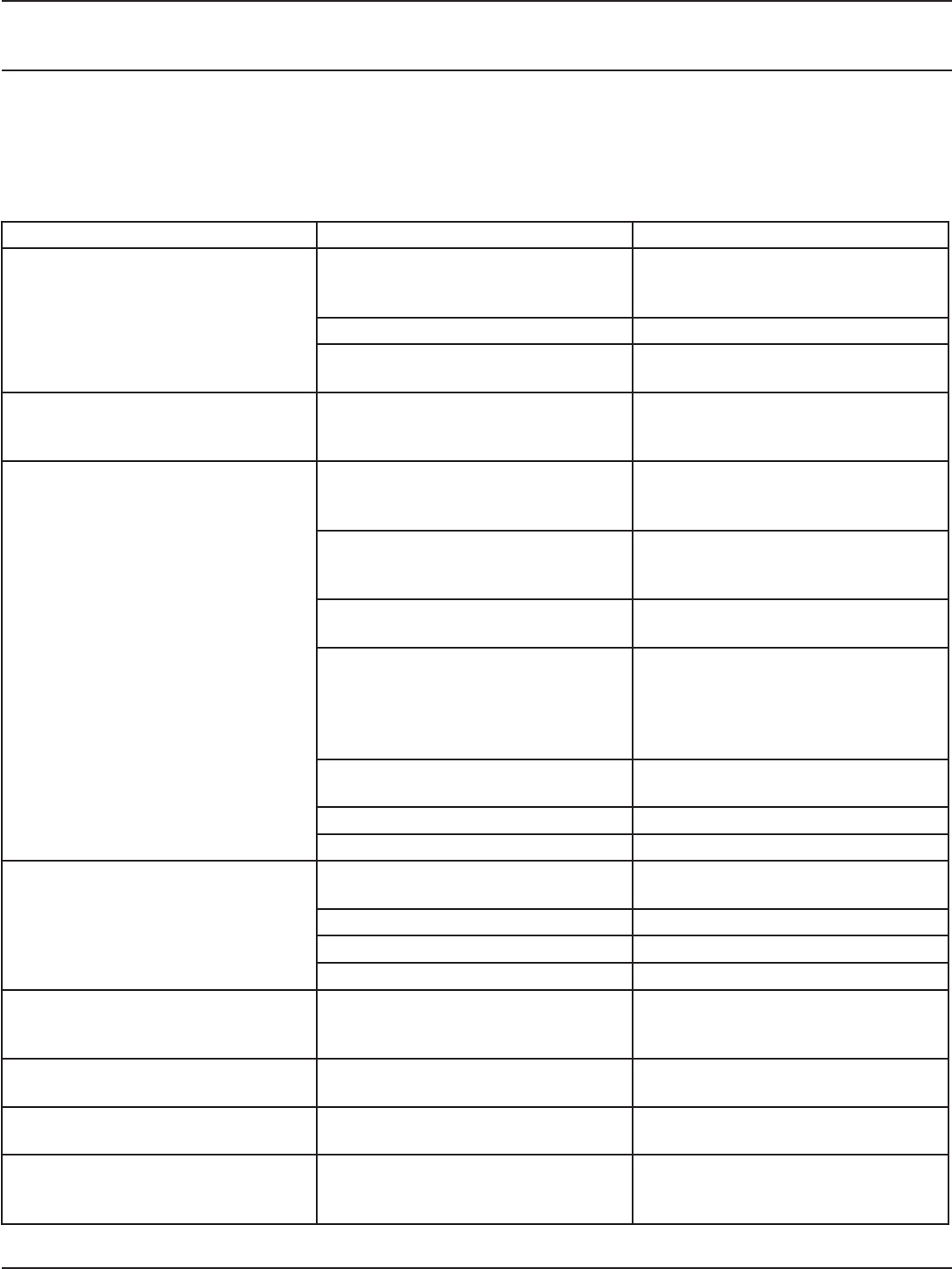
20
TROUBLESHOOTING
If symptoms of poor performance develop, the following
chart can be used as a guide to correct the problem.
When diagnosing faults in operation of the tool, always
check that the hydraulic power source is supplying the
correct hydraulic fl ow and pressure to the tool as listed
in the table. Use a fl owmeter known to be accurate.
Check the fl ow with the hydraulic oil temperature at least
80°F/27°C.
SYMPTOM CAUSE REMEDY
Tool does not run. Hydraulic power source not function-
ing correctly.
Check power source for proper fl ow
and pressure (7-9 gpm26-34 lpm at
2000 psi/140 bar.
Coupler or hoses blocked. Remove obstruction.
Mechanical failure. Have tool serviced by authorized
dealer.
Tool runs backwards. Pressure and return lines incorrectly
connected.
Correct hose connections. Motor shaft
rotates counterclockwise as viewed
from the end of the motor shaft.
Diamond saw cuts slow. Insuffi cient fl uid fl ow or too high back
pressure or relief valve set too low.
Check hydraulic supply. If hydraulic
supply is correct, have unit serviced
by authorized dealer.
Back pressure too high. Should not exceed 250 psi/17 bar at
9 gpm/34 lpm measured at the end of
the tools operating hoses.
Loss of diamond segment side clear-
ance.
Replace chain.
Chain segment dulled because of con-
tinuous use in hard material or rebar.
Redress segmented by cutting in
abrasive material (i.e. concrete, build-
ing block, etc.).
Note: This indicates that the wrong
chain is being used.
Wrong chain for application. Scale down to a lower numbered
chain.
Wired edged bar rails. Dress rails square.
Hydraulic fl uid mixed in water supply. Have tool serviced.
Excessive vibration and cuts rough. Segment(s) broken or missing. Repair broken segment or replace
chain.
Chain installed backwards. Correct chain direction.
Loose chain tension. Retension the chain.
Excessive feed force. Reduce feed force.
Wil not cut straight. Accumulated saw bar wear and un-
even chain segment profi le wear.
Turn the saw bar over and dress rails
square. Replace the saw bar and
chain.
Loss of power. Drive sprocket slipping on Tran-
torque® adapter.
Adjust and tighten Trantorque®
adapter to 17 ft lb/23 Nm.
Trigger hard to press. Pressure & return hose reversed. Connect for proper fl ow direction. Mo-
tor shaft must rotate clockwise.
Back-pressure too high. Should not exceed 250 psi/17 bar @
9gpm/34 lpm measured at the end of
the tool’s operating hoses.