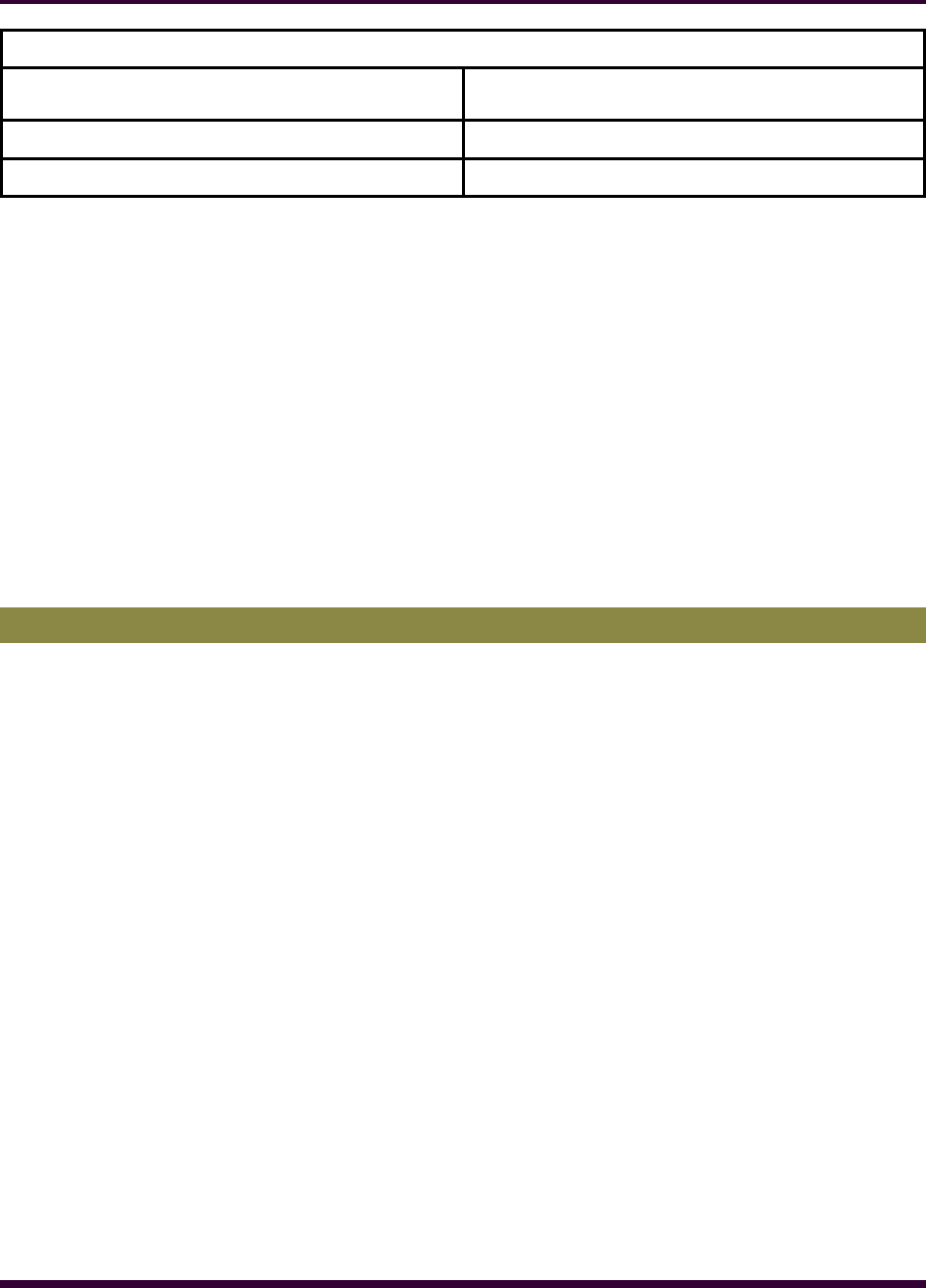
AR-EXP-CUMMINS-07-00 OWNERS MANUAL
Page 33
Cummins Inc. recommends using Fleetguard® Compleat. It is available in both glycol forms (ethylene and propylene).
Fully formulated antifreeze must be mixed with good-quality water at a 50/50 ratio (40- to 60-percent working range). A
50/50 mixture of antifreeze and water gives a -36°C [-33°F] freezing point and a 108°C [226°F] boiling point, which is
adequate for locations in North America. The actual lowest freezing point of ethylene glycol antifreeze is at 68 percent.
Using higher concentrations of antifreeze will raise the freezing point of the solution and increase the possibility of a silica
gel problem.
Do not use sealing additives in the cooling system. The use of sealing additives will:
• Buildup in coolant low-flow areas
• Plug the radiator and oil cooler Possibly damage the water pump seal.
Do not use soluble oils in the cooling system. The use of soluble oils will:
• Corrode brass and copper
• Damage heat transfer surfaces
• Damage seals and hoses.
9. ALTERNATOR
For safety purposes it is necessary that any testing or maintenance carried out on electrical machine are performed by
qualified and authorized personnel, and all operation must be performed when the machine is stopped, at ambient tem-
perature and disconnected from any supply source (including the auxiliary circuits such as the anti-condensation heaters).
Furthermore all measures must be taken to avoid restarting the gen-set during maintenance.
9.1. INSPECTION AND MAINTENACE INTERVALS
Inspection and maintenance should take into account the importance of the plant ambient conditions (dust etc.) and op-
erating conditions.
As a general rule, the machine should be subjected to a first inspection after approx. 500 operating hours (in any case not
more than 1 year) and subsequent inspections when performing maintenance on prime mover.
When performing inspection check that:
• The generator operates smoothly, without noise or irregular vibrations due to bearing deterioration
• The operating data complies with that detailed on the rating plate
• The air inlet openings are not obstructed
• The supply cables show no signs of deterioration and connections are firmly tight
• The electrical connections are in perfect condition (undamaged)
• Screws and nuts are firmly tightened.
9.2. MAINTENNCE OF BEARINGS
The lifetime of bearings is determined by multiple factors and specifically by:
• The lifetime of the grease. ·
• The environmental conditions and working temperature.
• The external loads and vibrations.
The bearings (D.E. and N.D.E. side are prelubricated sealed type (life lubrication), with sufficient grease quantity for a long
operating
time.
The life expected time is, in case of normal operating condition, of about 20000 hours for all bearings.
Water Quality
Calcium Magnesium
(hardness)
Maximum 170 ppm as
(CaCO
3
+ MgCO
3
)
Chloride 40 ppm as (CI)
Sulfur
100 ppm as (SO
4
)