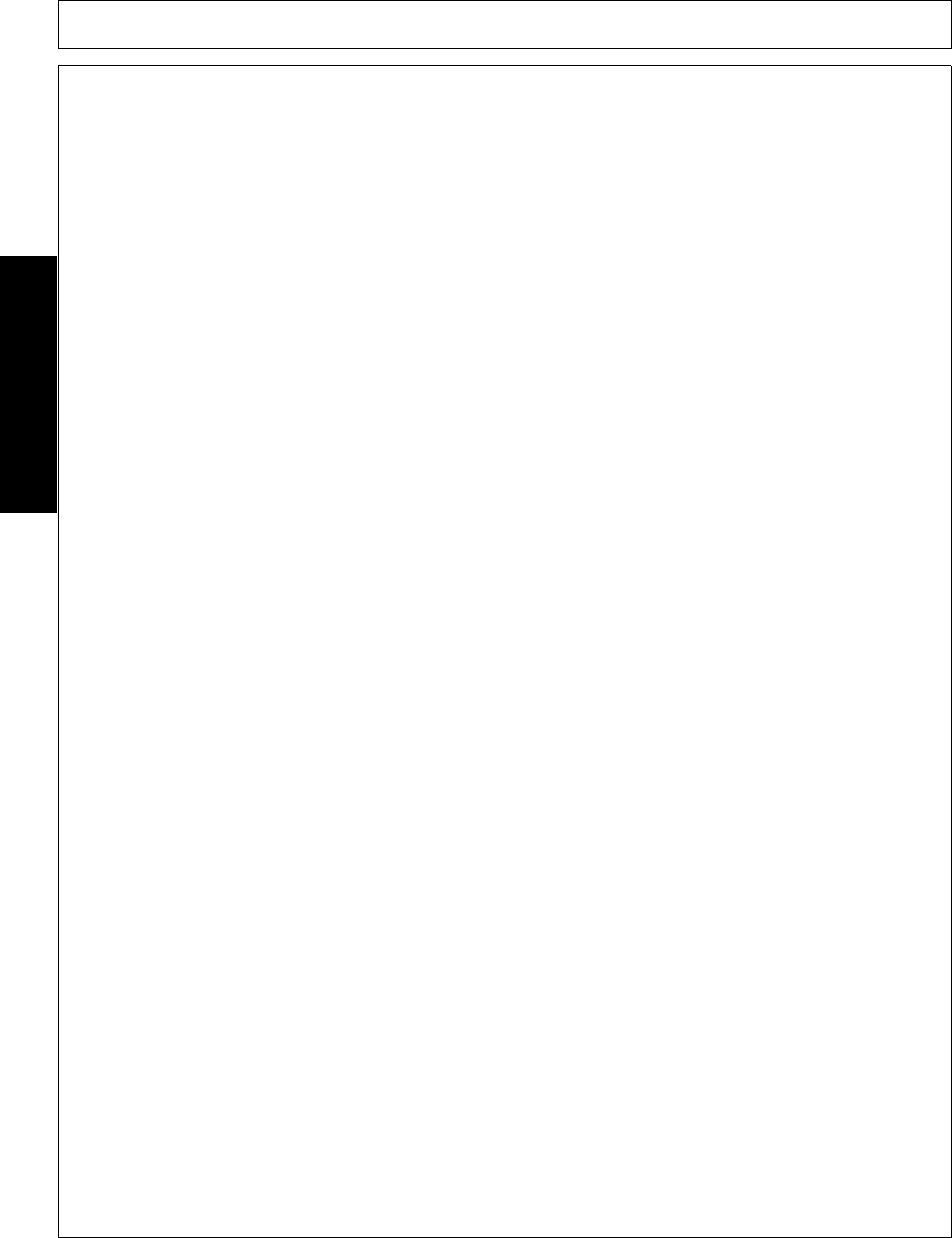
OPERATION
2160 06/11 Operation Section 4-48
© 2011 Alamo Group Inc.
OPERATION
Problem Possible Cause Remedy
Spindle Leaking At
Motor
Due to Motor Seal Failure
(hydraulic Oil leak)
See section on motor seal failure and repair as
needed
Motor Loose or bolts
missing
Bolts should be checked every 8 hrs. Loss of
torque will result in seal failure and leakage
Gasket torn due to
movement of motor on
s
p
indle flan
g
e
See above
Excessive Backpressure in
Spindle
Remove the Spindle vent plug and check for
clogs or contamination.
Spindle Leaking
Around Bottom Seal
Seal Damaged due to
Debris
Replace as required. Check for damaged or
missing seal guard
Bearings Loose Disassemble the Spindle and inspect the
bearings for damage. Re-assemble and
properly pre-load the bearings based on the
technical service manual.
Seal blown out due to
excessive back pressure
Remove the Spindle vent plug and check for
clogs or contamination.
Spindle Leaking At
Relief Vent
Relief fitting installed in the
fill hole (wrong hole)
Install the vent in the top most hole or even
with the top of the top bearing race. The lower
hole is the fill hole and should have a grease
zerk or plug installed.
Spindle Overfilled Overfilling will result in the lubricating oil being
expelled from the vent.
Spindle Overheating
Low Grease Level in the
spindle
Fill lubricant until it can be seen in the top most
(vent plug) hole.
Excessive Bearing Pre-
load
Disassemble the spindle and inspect the
bearings for wear. Re-assemble following the
bearing pre-load specifications in the Technical
Service Manual.
Blade bar bolts are too
long
Installing the incorrect bolts (too long) for the
blade carrier will allow the bolts to contact the
lower bearing and will lock up the spindle.
Install the correct bolts.
Spindle Shaft Loose or
Falls Out
Bearing Pre-load adjusting
nut and/or lock nut failure
Locking washers are provided to retain the pre-
load lock nut in place. Improper installation of
the washer and locking mechanism will allow
the lock nuts to back off. Re-assemble
following the recommended procedures
Bearing cups or cones not
installed properly
Disassemble and check for wear. Follow
reassembly procedures indicated in the
Technical Service Manual
Severe upper bearing
failure.
Usually due to lack of lube. Replace the
bearing(s) and make sure the spindle is
properly filled. Also check for leakage and
repair as needed.