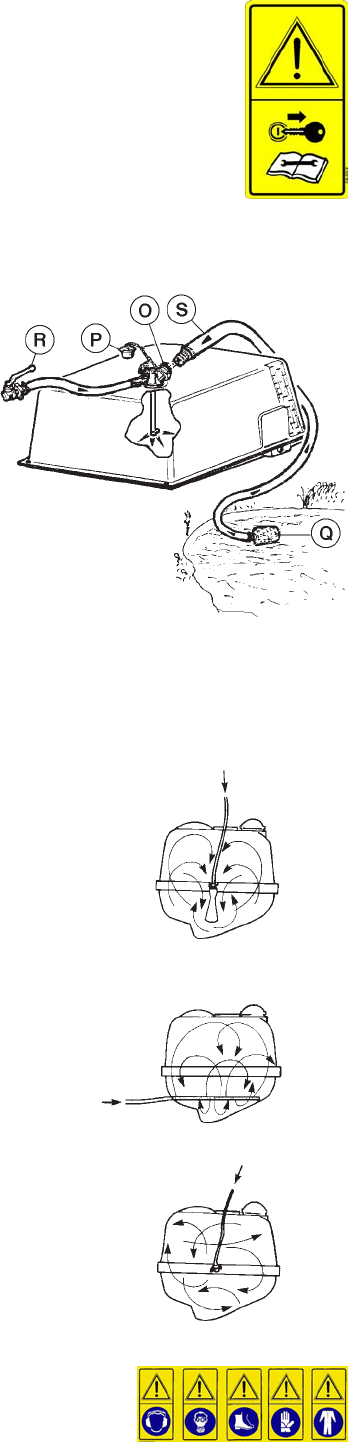
12
FIG. 6
4.10 FILLING THE TANK
The machines for defensive crop treatments, in consideration of the safety of
persons, animals and the protection of the environment, must only be filled
indirectly from open water courses and only by free-falling water from the
waterworks.
The pipe used for filling must never come into contact with the liquid inside
the tank and therefore the water must always fall over the upper edge of the
filling inlet and through the filter installed on it.
The tank is fitted with a transparent graduated band that shows the exact
quantity of liquid inside. This reading is precise if the tank is on flat ground;
the actual total capacity coincides with the highest number. All the filling
systems fitted by Unigreen on their production machines or on request are
antipollution and stop the liquid overflowing out of the tank.
4.10.1FILLING WITH THE ANTIPOLLUTION EJECTOR (FIG. 6)
If you are filling with an antipollution hydroejector (mounted as standard on
some models) then you should proceed as follows:
= put roughly 20-30 L of water in the tank and start the pump.
= remove the cap of ejector P and insert filling pipe S.
= place the other end of the hose, on which you fitted filter Q, in the
watering point.
= open the tap R that supplies the ejector (on pump or pressure regulator ).
= increase the pressure until it reaches a value which is sufficient to suck
up the liquid.
= visually check the level of the liquid inside the tank and after filling
disconnect pipe S from the ejector, close the tap R and replace the cap P.
4.11 TEST TREATMENT WITH CLEAN WATER
We recommend doing a test treatment with clean water to get to know the
system and check the settings.
4.12 MIXING
The active principle can be mixed using the relevant stirrers before and during
the treatment. Correct mixing and stirring is the basis of the correct
distribution on the crops. We recommend some useful accessories such as
the premixer for powders and liquids (see the following paragraph).
To mix the product in the tank proceed as follows:
a) high-pressure machines from 30 to 60 bar (FIG. N° 7): run the stirrer (or
ejector) for roughly 10-15 minutes at the maximum pressure available
b) low pressure machines, max 20 bar
= with a drilled pipe on the drain, run the pump at roughly 540 RPM with the
pressure regulator on drain for at least 10-15 minutes. (FIG. N° 8)
= with the stirrer on a delivery, run the pump supplying the stirrer (or ejector)
at the maximum pressure available for at least 10-15 minutes. (FIG. N° 7)
Some models with very small tanks aren’t equipped with mixers, you should
use the drain of the pressure regulator: run the pump at roughly 540 RPM with
the pressure regulator in the drain position for at least 10-15 minutes. (FIG.
N° 9).
4.12.1MANUAL PREMIXING
Dilute the active principle by hand before introducing it into the tank, (you
must wear suitable protective clothing such as rubber gloves, a mask or
goggles, overalls, etc.).
4.12.2PREMIXER ON COVER (OPTIONAL):
Open the cover and pour all of the chemical powder into the filter, close the
cover and open the supply tap until all of the powder has dissolved.
FIG. 7
FIG. 8
FIG. 9
WARNING: using the taps on the pump or in
any case on the front of the machine puts the
operator near the cardan shaft. Despite the
presence of CE standard protective covers
you should take great care.