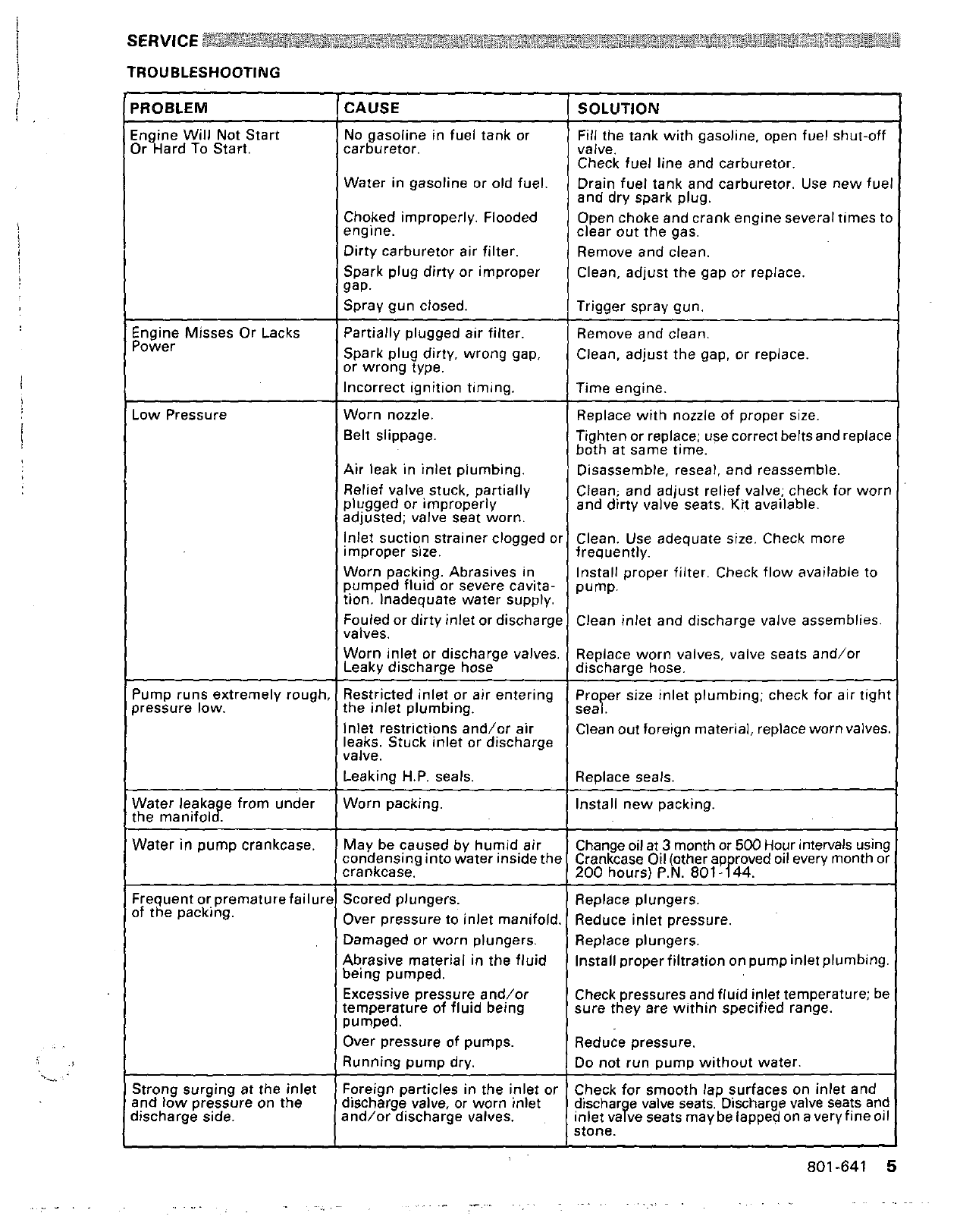
.i
..
.,-
'
'ROBLEM
ingine Will Not Start
)r Hard To Start.
Engine
Misses
Or Lacks
'ower
.ow Pressure
'ump runs extremely rough
)ressure low.
Nater kaka
e
from under
he manifolcf!
Nater
in
pump crankcase.
'requent orprematurefailurl
)f
the packmg.
strong surging at the inlet
nnd low pressure on the
lischarge side.
CAUSE
carburetor.
No gasoline in fuel tank or
Water in gasoline or old fuel.
engine.
Choked improperly. Flooded
Dirty carburetor air filter.
Spark plug dirty or improper
Spray gun closed.
Partially plugged air filter.
gap.
Spark plug dirty, wrong gap,
or wrong type.
Incorrect ignition timing.
Worn nozzle.
Belt slippage.
Air leak in inlet DlUmbing
.
Relief valve stuck, partially
adjusted; valve seat worn.
plugged or improperly
Inlet suction strainer clogged
01
improper size.
Worn packing. Abrasives in
pumped fluid or severe cavita-
tion. Inadequate water supply.
valves.
Fouled or dirty inlet or dischargf
Worn inlet or discharge valves.
Leakv discharge hose
the inlet plumbing.
Restricted inlet or air entering
Inlet restrictions and/or air
valve.
leaks. Stuck inlet or discharge
Leaking H.P. seals.
Worn packing.
condensing into water Inside
the
May be caused by humid air
crankcase.
Scored plungers.
Over pressure
to
inlet manifold
Damaged or worn plungers.
Abrasive material
in
the fluid
being pumped.
Excessive pressure and./or
temperature of fluld bemg
pumped.
Over pressure of pumps.
Running pump dry.
discharge valve, or worn inlet
Foreign particles
in
the inlet or
and/or discharge valves.
SOLUTION
Fill the tank with gasoline, open fuel shut-off
valve.
Check fuel line and carburetor.
Drain fuel tank
and
carburetor.
Use
new fuel
and dry spark plug.
clear out the gas.
Open choke and crank engine several times
to
Remove and clean.
Clean, adjust the gap or replace.
Trigger spray gun.
Remove and clean.
Clean, adjust the gap, or replace.
Time engine.
Replace with nozzle of proper size.
Tighten or replace; use correct beltsand replace
both at same time.
Disassemble, reseal, and reassemble.
Clean, and adjust relief valve; check for worn
and dirty valve seats. Kit available.
Clean. Use adequate size. Check more
frequently.
Install proper filter. Check flow available to
pump.
Clean inlet and discharge valve assemblies.
Replace worn valves, valve seats and/or
discharge hose.
Pro er
size
inlet plumbing; check for air tight
sear
Clean out foreign material, replace worn valves.
ReDlace seals.
Install new packing.
Change oil at
3
month or
5CO
Hour intervals using
Crankcase
Oil
(other ap roved oil every month or
200
hours) P.N.
801-r44.
Replace plungers.
Reduce inlet pressure.
Replace plungers.
Install proper filtration on pump inletplumbing.
Check pressures and fluid inlet temperature; be
jure they are within specifled range.
?educe pressure.
30
not run pump without water.
:heck for smooth lap surfaces on inlet and
$ischar e valve seats.
Discharge
valve seats and
nlet vabe seats mavbe lapped on a veryfineoll
;tone
801-641
5
..
.
.
..
..
.
.
.~~
... ".
.
.
...
..