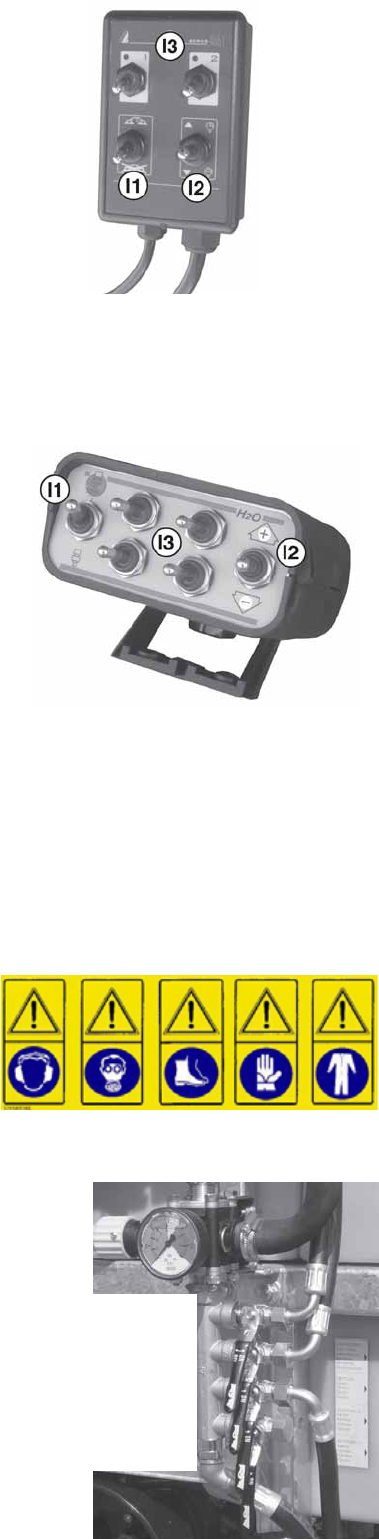
unigreen 13
= adjust maximum pressure valve B to the working value (in any case less
than the safe maximum pressure the system can reach).
Pressure regulators with a volumetric valve (GCP ELETTRICO)
Adjusting the maximum pressure valve
= put main control A in the drain position (“OFF”).
= loosen the hand wheel of maximum pressure valve B completely
(anticlockwise).
= open volumetric valve E completely.
= start the pump by activating the power-takeoff of the tractor at 540rpm
= open main control A (position “ON”), the manometer will be activated
= open the drain tap on filter F slightly (only GCP ELETTRICO).
= close volumetric valve E completely. If the pressure rises over the maximum
limit of the system, make sure maximum pressure valve B is open (see previous
indications)
= open all of the section valves C (position “ON”)
= adjust maximum pressure valve B to a value over that of the working
pressure (generally 10-14bar) and in any case lower than the safe maximum
pressure that the system can reach.
Adjusting the volumetric pressure.
= with the volumetric pressure valve E adjust the pressure to the value the
treatment will be done at (the pressure is indicated on the nozzles tables on the
basis of the tractor speed and litres/hectare to spray)
Warning! The working pressure must be adjusted with the volumetric valve
and not with the maximum pressure valve. In the case the working
pressure is too near to the calibrated pressure of the maximum pressure
valve, the proportional valve may not be able to compensate the speed
variations correctly.
Adjusting the compensated returns
= close only one tap of section C (position “OFF”).
= adjust the corresponding compensator G until you return to the pressure set
previously (displayed on the manometer).
= open and close the tap of section C and check that the pressure remains
constant.
= repeat the above operations for all the section taps.
If the types of nozzles aren’t changed the regulations carried out will guarantee a
constant spraying of the liquid also per treatments that are done at different
working pressures.
NB: if the type of nozzle is changed then the calibrating will have to be done
again.
4.8.3 DELIVERY FILTERS (ONLY EQUIPPED MODELS)
This is particularly useful when using small nozzles (low volume), they are
normally mounted on the jet booms and have a filter cartridge with a 40-gauge
mesh (the equivalent of a 0.4 mm hole).
At the end of each treatment cycle you should clean the cartridge: turn the jets to
the closed position, put the command under pressure and open the tap under
the filter to drain the tank for a few minutes.
You should clean the cartridge by hand periodically, on the basis of the product
used. Stop the pump to clean. Wear rubber gloves and the other personal
protective equipment when cleaning.
4.9 AUXILIARIES TAPS BLOCK
A collector is installed (FIG. 9) in the machines with taps for the utilities and
accessories, which require a working pressure that is independent from the
spraying pressure:
- Tank washing jet: see paragraph 4.13.1
- Ejector: see paragraph 4.10
- Agitators (2 independent taps): see paragraph 4.12
The taps are identified by the relevant sticker and the methods of use are
described in the paragraphs indicated.
The pressure is normally regulated to 30-35 bar with the relevant valve (using a
yellow knob) and displayed on the manometer installed; opening the utilities
makes the pressure drop.
FIG. 9
Tank rinsing
Ejector
Agitator 1
Agitator 2