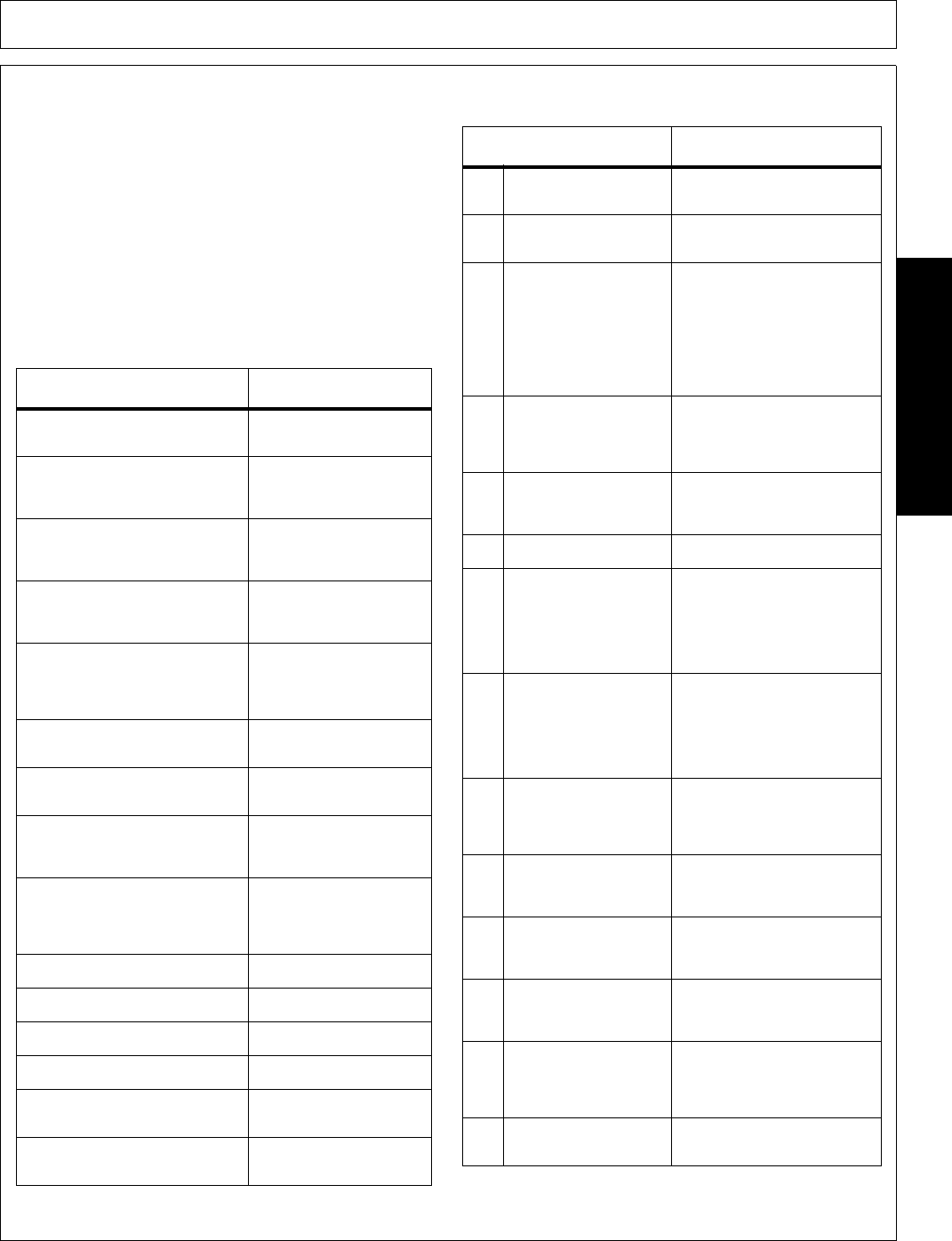
MAINTENANCE
F-4139 01/11 Maintenance Section 3-5
© 2011 Alamo Group Inc.
MAINTENANCE
HYDRAULIC TROUBLESHOOTING
Hydraulic troubleshooting material presented in this section
is offered as a guide to diagnosing probable causes and
remedies for general operational problems.
Match your problem wiht the typical problem examples
given in the possible cause column. These numbers
correspond with the possible cause and correction
paragraphs that follow.
NOTE: If, when using the following chart, it is decided that
overhaul of components or pressure adjustment is
necessary, it is recommended that your dealer make these
repairs. He is equipped to do this work.
PROBLEM POSSIBLE CAUSE
Machine fails to operate
when initially started.
1, 2, 5, 7, 15, 23
Machine looses power after
initially operating
satisfactorily.
1, 8, 10, 15, 23
Loss of power in lift or crowd
cylinder, but other cylinders
function properly
22, 24, 28
Loss of power in any one
cylinder including lift and
crowd
8, 9, 10, 11, 12, 13, 22,
23, 25
Loss of power or loss of
cushioning action in swing
cylinders, but other cylinders
function properly.
8, 9, 10, 11, 12, 13, 22,
23, 25
Maximum swing action
cannot be obtained.
12, 14
Slow operation of machine
(lack of power) all cylinders.
1, 4, 6, 15, 23
Spongy or jerky action of
cylinders and/ or noisy
operation.
1, 3, 4, 5
Lift crowd or bucket cylinders
drop under load when lever
spools are shifted from
neutral.
26, 28
Load drops or settles. 8, 10, 13, 25, 26
Leaky cylinders. 10, 11, 12, 13
Leaky valve. 8, 15, 16, 27
Sticky valve spool. 16, 19, 20, 21
Unable to push valve spool
in.
16, 17, 20, 21
Spring centered spools do not
return to neutral.
16, 17, 18, 19, 20, 21
POSSIBLE CAUSE CORRECTIVE ACTION
1 Low oil level in
reservoir.
Fill reservoir to proper
level.
2 No oil supply to
machine.
Engage tractor PTO.
3 Air in system. Purge all circuits of air by
operating all cylinders
through full movements
several times. Check oil in
reservoir for foaming.
Check all suction lines for
leaks. Fill reservoir to
correct level.
4 Oil viscosity too
heavy or oil is not at
operating
temperature.
Use recommended
hydraulic fluid. Run
machine until it reaches
operating temperature.
5 Pump not running. Check PTO to be sure it is
engaged. Pump
connected to PTO.
6 Insufficient pumping. Advance engine throttle.
7 Improper hose
connection.
IMPORTANT: Be sure inlet
and return hoses are
hooked up correctly.
Improper hookup will
result in damage to
backhoe valve.
8 Loose hydraulic
connections, leaks
in fittings or hoses.
Tighten all hose
connections and replace
all damaged o-rings at
leaking o-ring fittings.
Check and replace any
damaged hoses.
9 Restriction in fittings
or hoses.
Check and replace any
damaged hoses and
fittings. Check for pinched
hoses.
10 Oil is bypassing
cylinder piston.
Replace or rebuild
cylinder. Replace
damaged parts.
11 Scored piston rods
or worn rod guides
in cylinder.
Replace or rebuild
cylinder. Replace
damaged parts.
12 Bent piston rod in
cylinder
Replace or rebuild
cylinder. Replace
damaged parts
13 Worn or damaged
rod seals on
cylinder. External
leaks.
Re-pack cylinder. Rebuild
cylinder replacing
damaged parts as
necessary.
14 Swing linkage
jammed.
Remove interference.