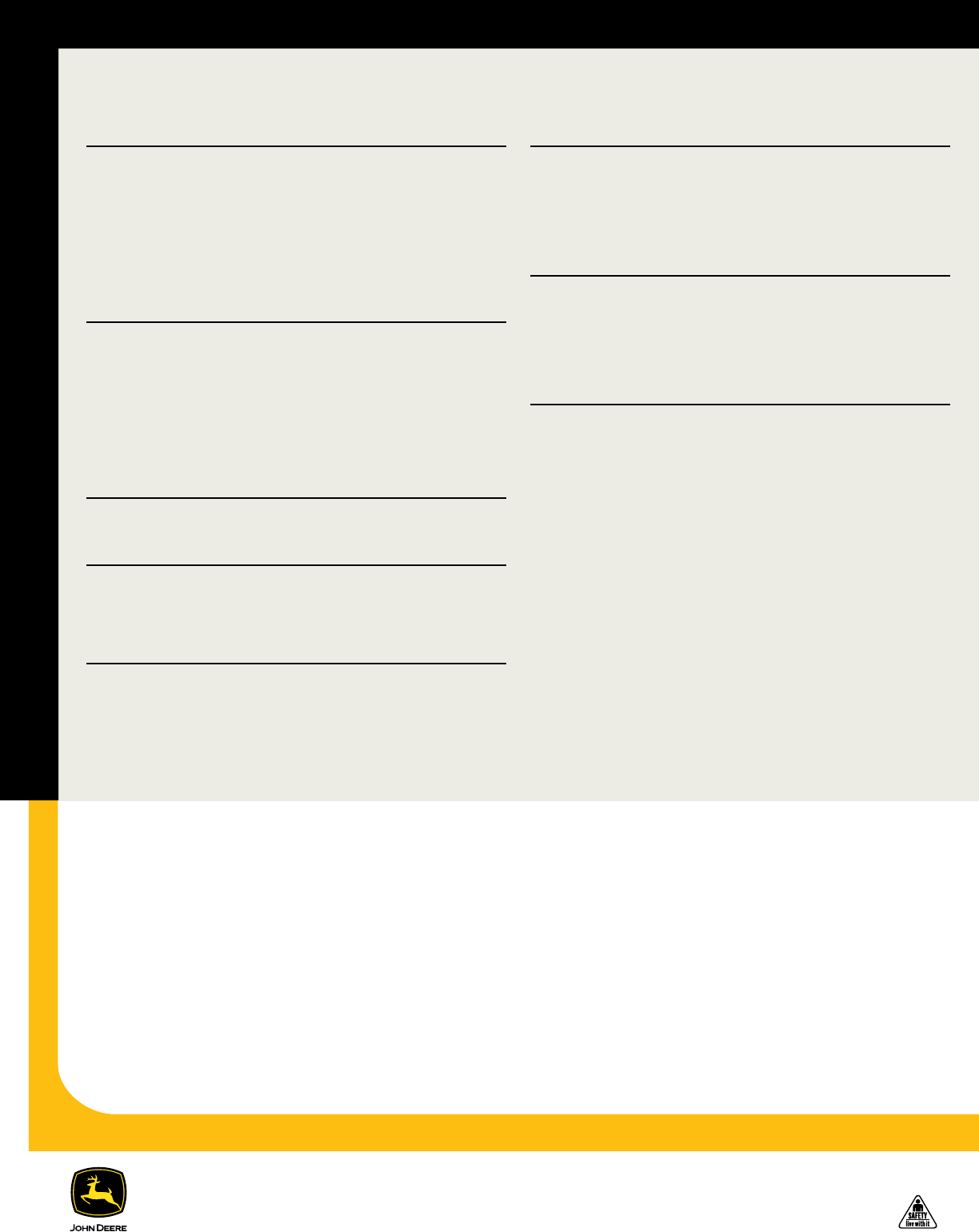
Net engine power is with standard equipment including air cleaner, exhaust system, alternator, and
cooling fan at test conditions per ISO9249. No derating is required up to 10,000-ft. (3050 m) altitude.
Also available: winches, fair-leads, log arches, skidding grapples, trash packages, landfill protection
packages, cable plows, side booms, field-installed cab for canopy, canopy heater, and fire suppres-
sion systems.
Specifications and design subject to change without notice. Wherever applicable, specifications are
in accordance with SAE standards. Except where otherwise noted, these specifications are based
on units with rollover protective structures, full fuel tanks, 175-lb. (79 kg) operators, and standard
equipment; 750J LT unit with 22-in. (560 mm) moderate-duty grousers, rigid drawbar, and Semi-U
(High-Production) blade; and 750J WT and LGP units with 34-in. (865 mm) single-bar grousers and
rigid drawbars.
10-05-09
750J 850J Engine
lCertified to EPA Tier 3 emissions
l Certified to EPA Tier 3 and EU Stage IIIA emissions
s Certified to EPA Tier 2 and EU Stage II emissions
l l Electronic control with automatic engine protection
l l Dual safety element dry-type air cleaner, evacuator valve
l l Muffler, self draining, under hood, with vertical stack
l l Environmental service drains
s s Ether start aid
s s Chrome exhaust
s s Rotary ejector engine air precleaner
Cooling
l l Cooling fan, suction type, programmable reversing
lEngine coolant radiator (10 fins per in.)
l Engine coolant radiator (6 fins per in.)
lHydrostatic cooler (oil/air – 10 fins per in.)
l Hydrostatic cooler (oil/air – 6 fins per in.)
l l Hydraulic cooler (oil/air – 6 fins per in.)
l l Enclosed safety fan guard (conforms to SAE J1308 and ISO3457)
l l Perforated engine side shields
l l Split-hinge bar-type grille
s s Extreme-duty grille
Transmission
l l Diagnostic test ports
l l Environmental service drains
s s Final-drive seal guards
Hydraulic System
l l Two-function hydraulics
s s Three-function hydraulics
s s Four-function hydraulics with rear plumbing
s s High-flow hydraulic pump and hydraulic cooler for use with winch
s s Integrated Grade Control (IGC)
Mainframe, Access Panels
l l Tilt operator station transmission access
l l Front tow loop (bolt-on)
l l Integral bottom protection
l l Hinged bottom access covers (bolt-on)
l l Vandal protection: Engine access door / Side tank access doors / Fuel
tank / Instrument panel / Transmission reservoir / Hydraulic reservoir
l l Maintenance-free center crossbar pivot
750J 850J Attachments
s s Retrieval hitch with pin
s s Extended rigid drawbar with pin for pull-type implements
s s Counterweight, rear, 720 lb. (327 kg)
s s Counterweight, rear, 1,000 lb. (454 kg)
s s Ripper, rear, three shank
s s Winch, hydrostatically driven*
s s Forestry screens*
Undercarriage
l l Oscillating undercarriage with remote lube
l l Full-length, smooth-surface track frame covers
l l Guides, front and rear, with bolt-on wear strips
l l Segmented sprockets
l l Double-flange rollers
s s Extended life undercarriage SC-2
TM
bushings
s s Full-length rock guards
Canopy Cab
Operator’s Station / Electrical
l l Retractable seat belts, 3 in. (76 mm) (conforms to SAE J386)
l l Convex interior rearview mirror, 4-in. (102 mm) tall, 8-in. (203 mm)
wide (conforms to SAE J985)
l l Power port, 12 volts
s s Second power port, 12 volts
l l Lockable dash-mounted storage compartment
l Air conditioner, 24,000 Btu
l Tinted glass
l Dome light
l Heater (roof mount)
l Front and door wipers
l Mechanical suspension vinyl seat
l Mechanical suspension fabric seat
s Air suspension vinyl seat
s Air suspension fabric seat
s Under-seat heater
s Rear wiper, two speed
s AM/FM, weather-band radio, clock
s External-mounted attachment mirror
l l Sealed alternator, 55 amps
l l Master electrical disconnect switch
l l Lights, grille mounted (2), rear mounted (1)
s s Work lights (4), roof mounted
l l JDLink
TM
Ultimate wireless communication system
750J / 850J CRAWLER DOZERS
Key: l Standard equipment s Optional or special equipment *See your John Deere dealer for further information.
CONTROL OWNING AND OPERATING COSTS
Customer Personal Service (CPS) is part of John Deere’s proactive, fix-before-fail
strategy on machine maintenance that will help control costs, increase profits, and
reduce stress. Included in this comprehensive lineup of ongoing programs and ser-
vices are:
Fluid analysis program – tells you what’s going on inside all of your machine’s
major components so you’ll know if there’s a problem before you see a decline in
performance. Fluid analysis is included in most extended coverage and preventive-
maintenance agreements.
Component life-cycle data – gives you vital information on the projected life
span of components and lets you make informed decisions on machine maintenance
by telling you approximately how many hours of use you can expect from an
engine, transmission, or hydraulic pump. This information can be used to preempt
catastrophic downtime by servicing major components at about 80 percent of
their life cycle.
Preventive Maintenance (PM) agreements – give you a fixed cost for main-
taining a machine for a given period of time. They also help you avoid downtime
by ensuring that critical maintenance work gets done right and on schedule. On-
site preventive maintenance service performed where and when you need it helps
protect you from the expense of catastrophic failures and lets you avoid waste-
disposal hassles.
Extended coverage – gives you a fixed cost for machine repairs for a given
period of time so you can effectively manage costs. Whether you work in a severe-
service setting or just want to spread the risk of doing business, this is a great
way to custom-fit coverage for your operation. And an extended coverage contract
also travels well because it’s backed by John Deere and is honored by all Deere
construction dealers.
Customer Support Advisors (CSAs) – Deere believes the CSA program lends
a personal quality to Customer Personal Service (CPS). Certified CSAs have the
knowledge and skills for helping make important decisions on machine mainte-
nance and repair. Their mission is to help you implement a plan that’s right for
your business and take the burden of machine maintenance off your shoulders.